Die Industrie 4.0 hält Einzug in die Pavese AG
Manuelle Produktionsabläufe benötigen vor allem eins: viel Zeit. Das ist auch in der Pavese AG, einem Präzisionsmechanik-Betrieb in Schenkon, nicht anders. Dank der neu erarbeiteten smarten Maschinendatenerfassung hat sich dies nun geändert.
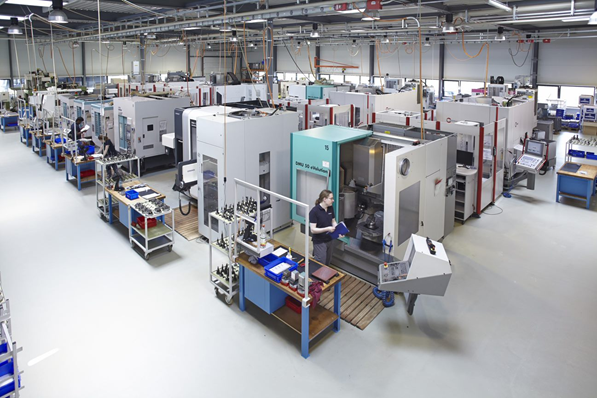
Fräsen, Drehen, Schleifen: In der Pavese AG in Schenkon dreht sich alles um die Herstellung von hochpräzisen Teilen. Das KMU mit über 20 Mitarbeitenden, geführt von den Brüdern Enzo und Daniele Pavese, ist ein klassischer Familienbetrieb. Gegründet wurde das Unternehmen 1978 von Rocco Pavese, dem Vater der beiden, der die Pavese AG damals in Nottwil als mechanische Werkstatt und Schlosserei aufgebaut hat.
Die hier in Schenkon hergestellten Produkte werden zu einem grossen Teil in der Medizinaltechnik verwendet. Aber auch in der Halbleiterindustrie, in der Luft- und Raumfahrttechnik sowie in der Maschinenindustrie finden die Produkte Einzug. Was die Pavese AG ihren Kunden dabei bereitstellt, ist eine umfassende Dienstleistung: Vom Beschaffen des Rohmaterials bis hin zum fertigen Produkt (Prototypen, Einzelteile oder komplexe Baugruppen) setzen die Mitarbeitenden der Pavese AG die Wünsche ihrer Kunden um. Was das Familienunternehmen dabei auszeichnet, ist die ausserordentlich hohe Qualität – der Mitarbeitenden, des Maschinenparks, der Produkte.
Von manuell zu smart
Dass die Welt durch die Digitalisierung im Wandel ist, merkt man auch hier in Schenkon. Dieser Tatsache begegnet die Pavese AG mit Offenheit und Tatendrang. Denn die Chancen der Digitalisierung werden erkannt: Dank ihr wird eine effizientere Gestaltung der Produktion möglich. Mit Unterstützung des RET (Regionaler Entwicklungsträger Sursee-Mittelland) konnte die Pavese AG nun einen überbetrieblichen und neuartigen Projektansatz verfolgen, der von einer breiten Trägerschaft dreier Unternehmen (nebst der Pavese AG die CyberTech Engineering GmbH und ProALPHA Schweiz AG) sowie weiteren Partnern (Swiss Smart Factory und die Firma Erowa aus Büron) getragen wird.
Das Ziel des Projekts lag in der direkten Vernetzung des IT-Systems mit den Produktionsmaschinen. Das Resultat, das auch anderen Unternehmen zur Verfügung gestellt wird, lässt sich sehen: Erarbeitet wurden ein Konzept und eine Software, mit deren Hilfe Plan- und Auftragsdaten direkt auf die Werkzeugmaschinen übertragen werden. So konnte im Rahmen des Projektes eine 5-Achsen CNC Fräsmaschine direkt mit dem ERP System vernetzt werden. Diese ist nun in der Lage, Daten wie z.B. Stückzahlen und NC Programm bidirektional auszutauschen. Auf diese Weise wird die Produktivität erhöht und die Wettbewerbsfähigkeit des Standorts gesteigert. Langfristig wirkt sich dies positiv auf die Beschäftigung aus: Durch einen möglichen Ausbau der Produktion werden nicht nur Arbeitsplätze gesichert, sondern auch das Schaffen von neuen Arbeitsplätzen wird erleichtert.
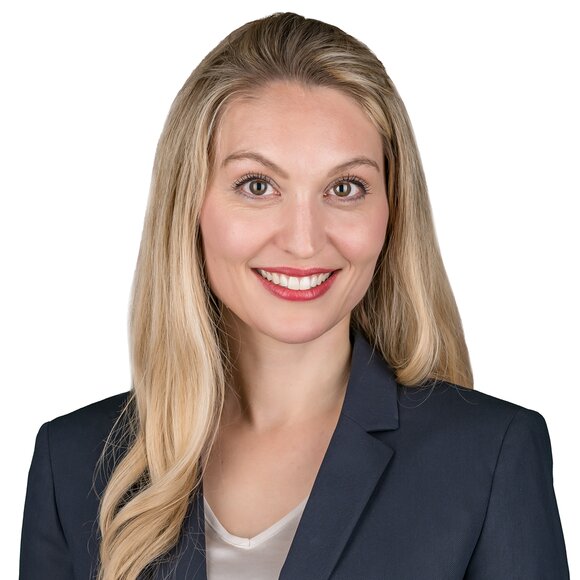
Anja Hammerich
Projektleiterin Kommunikation/Content
Telefon +41 41 367 44 08
- Kommunikation
- Content Manager